Choosing the right battery charger solution for your operation is just one piece of the puzzle. Configuring output cable management to protect your equipment will help maximize the performance and longevity of your charging systems. There are many methods of cable management in use across the industry, but our first pick here at Stanbury Electrical Engineering is the compact and clever TBR-15 Cable Retractor.
What is the TBR-15 Cable Retractor?
The Stanbury TBR-15 Cable Retractor is the ideal solution for safely managing charging cables for most charger setups. With over four feet of horizontal or vertical travel and up to 15 pounds of adjustable tension available, the TBR-15 Cable Retractor is one of the most adaptable cable management solutions on the market.
TBR-15 specifications:
- Braided steel cable, capable of over four feet of travel
- Adjustable spring tension to support a wide variety of cable lengths and gauges
- Inner spring rated to 100,000 retraction cycles – up to 30 years of use
- Rugged, industrial-grade retractor housing
As a specialist manufacturer of battery chargers, we know that selection and installation of a new charger is just the start. Warehouse equipment is often subjected to tough working conditions in the hands of operators who place more importance on efficient productivity than on gentle care of equipment. For a charger, the parts subjected to daily mechanical stress and the greatest potential for abuse are the output cables and connectors. When cables are not properly managed this leads to charger repair expense and presents the possibility of hazards to operators. We have seen just about every cable management combination over our more than sixty years in business, and often see the implications of getting it wrong.
Three reasons for good cable management
Maintenance Cost / Operator Safety / Facility Aesthetics
1. Reduce maintenance overheads
Less operational breakages equals lower ongoing maintenance costs, less machine downtime and less operator time wasted. The most common source of charger breakages are from cables dropped on the floor being damaged, or being hooked on vehicles without the operator noticing.
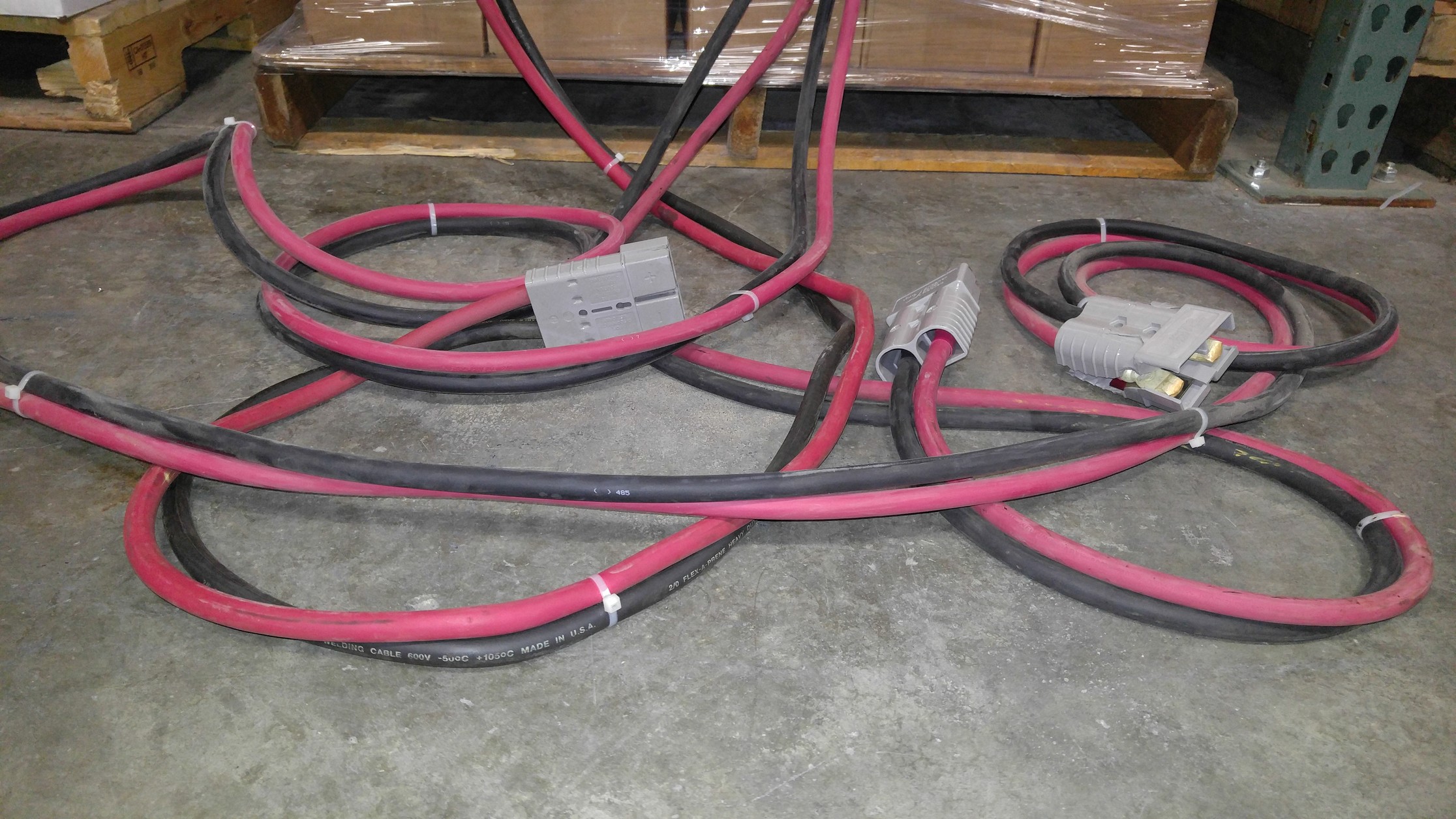
Although our charger electronics are built to a higher standard of rugged reliability, the battery connectors used are not within our design scope. The SB connector housing typically used on batteries will crack when dropped on the cement floor of a warehouse. Once on the floor, they are also at risk of breakage from being stepped on or run over. Cable management systems like the TBR-15 Cable Retractor keep the charger’s output connectors off the ground and away from machinery, wheels and operator boots.
Cable retractors also keep the charging cables themselves off the floor and away from being run over, stepped on or tripped over. This in turn helps avoid cable insulation damage, which can pose a significant arc or explosion hazard when the charger connects to a battery. The TBR-15 Cable Retractor also helps prevent the charger cables from being entangled with the vehicle mast, which often results in a charger being pulled down off its mounting or ripped apart at its output terminals as the vehicle drives away.
Although replacing cables and their connectors isn’t the largest expense a fleet operator faces, it adds up over time if breakages happen frequently – as does the associated downtime for vehicles and chargers alike. This doesn’t have to be the norm.
Cable management systems such as the TBR-15 Cable Retractor keep your charging cables tidy and out of harm’s way, and the robust build of the unit means it will outlast similar pogo retractor solutions.
Also consider mounting your chargers on our pedestal stands or triangle wall brackets to further reduce opportunities for cable damage to occur.
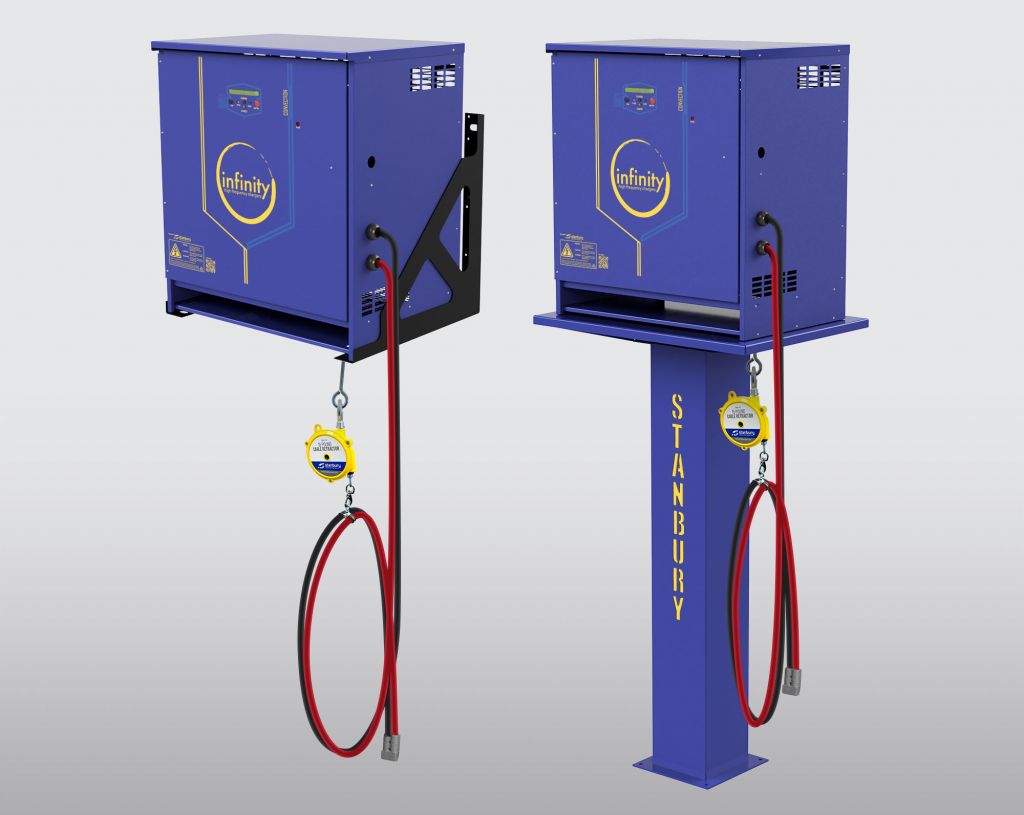
2. Operator safety while using battery chargers
There is a more serious implication associated with charger cables being left on the ground or thrown over the top of charger units: operator safety. Cluttered cables are a trip and entanglement hazard. They can be ripped from the unit and expose live wires, or the charger itself can be damaged or fall over. This could result in exposed live wires, or worse.
Even without accidents occurring, the increased wear and tear on cables and connectors from being frequently tangled and dragged across concrete can result in live wires being exposed over time.
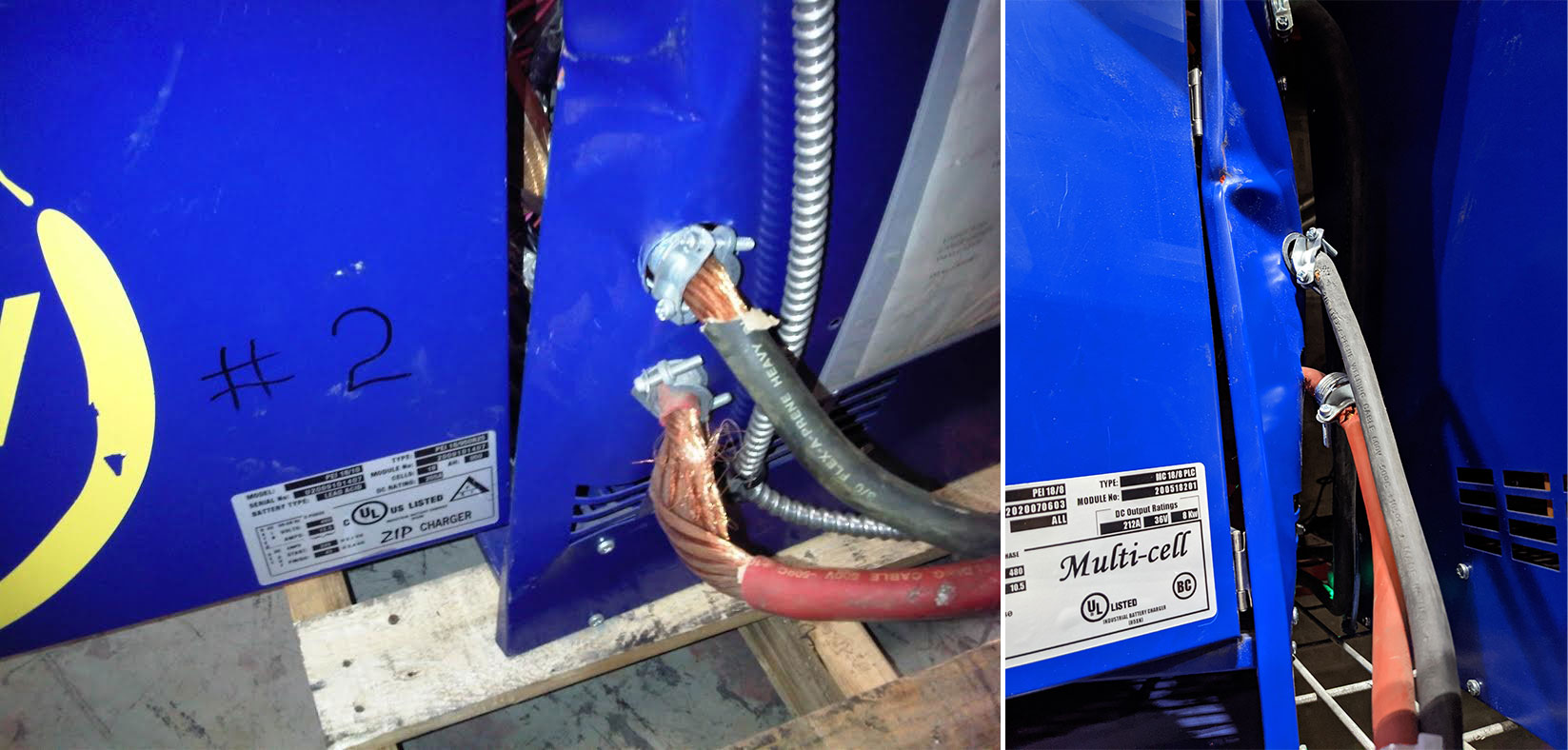
Safety is the aspect we at Stanbury Electrical Engineering take most seriously when it comes to cable management. This is why we recommend the TBR-15 Cable Retractor and its mounting solutions so strongly. Reducing the opportunity for trip and entanglement accidents by keeping chargers and their cables off the ground will drastically improve operator safety when interacting with their chargers.
3. Aesthetics: more than just tidy cable management
While a flawlessly beautiful and sterile operational space isn’t critical for the bottom line, a cluttered charging area will certainly have a negative impact. More than just looks, aesthetics serve several key functions.
Allowing sufficient space for vehicles to park: space comes at a premium for many sites, especially space designated for vehicle downtime. The more compact, tidy and fuss-free the cable management solution, the less room vehicles require and the less likely some charging stations will be favored over others.
Reducing cable clutter: keeping cables off the floor and keeping them from becoming entangled with each other has implications beyond maintenance and safety. Along with keeping the rest of the workplace orderly and organized, it can have a psychological effect on operators and influence the care they take in their work and the respect they show their equipment. Good cable management can reduce operator frustration and rough handling, and thus reduce maintenance costs and safety concerns.
Carefully considered cable routing: designing your charging workflow from the ground up has several positive implications. Ease of access for operators and making it immediately obvious where and how cables should run between the charger and the battery leads to less opportunities for cables to become entangled in vehicles, and more consistent correct use by operators.
How can something so simple be so problematic?
Believe it or not, cable management is a surprisingly common oversight. In older battery changing systems with battery racks, the charging cables were typically fixed in place and were not exposed to the same risks. Motive power battery charging has evolved rapidly over the last two decades. With the advent of opportunity charging for lead acid, and now fast charging for lithium batteries, there are more and more instances where the battery charges in the vehicle rather than on a battery rack. Often the shift to park and charge has not put sufficient focus on how best to manage the charger cables.
This is a problem that can be solved in a few ways. Here’s how the TBR-15 Cable Retractor measures up:
Charging cable management method | Pros | Cons |
---|---|---|
Do nothing |
|
|
Wall hook |
|
|
Pogo stick retractor |
|
|
Overhead arm |
|
|
TBR-15 cable retractor |
|
|
Where and how to install your TBR-15 Cable Retractor
The Stanbury TBR-15 Cable Retractor can be installed on any of our chargers, as well as others you may already have on site – whether you’re upgrading from pogo retractors, or getting cables off the warehouse floor.
The TBR-15 Cable Retractor can be mounted from the charger mounting bracket/stand, from above, or from the charger itself (the hanger bar option makes this simple). Consider the mounting of the charger itself and how the cables will be routed to vehicle batteries when planning where the retractor will be hung. Also consider where the cable will hang when retracted.
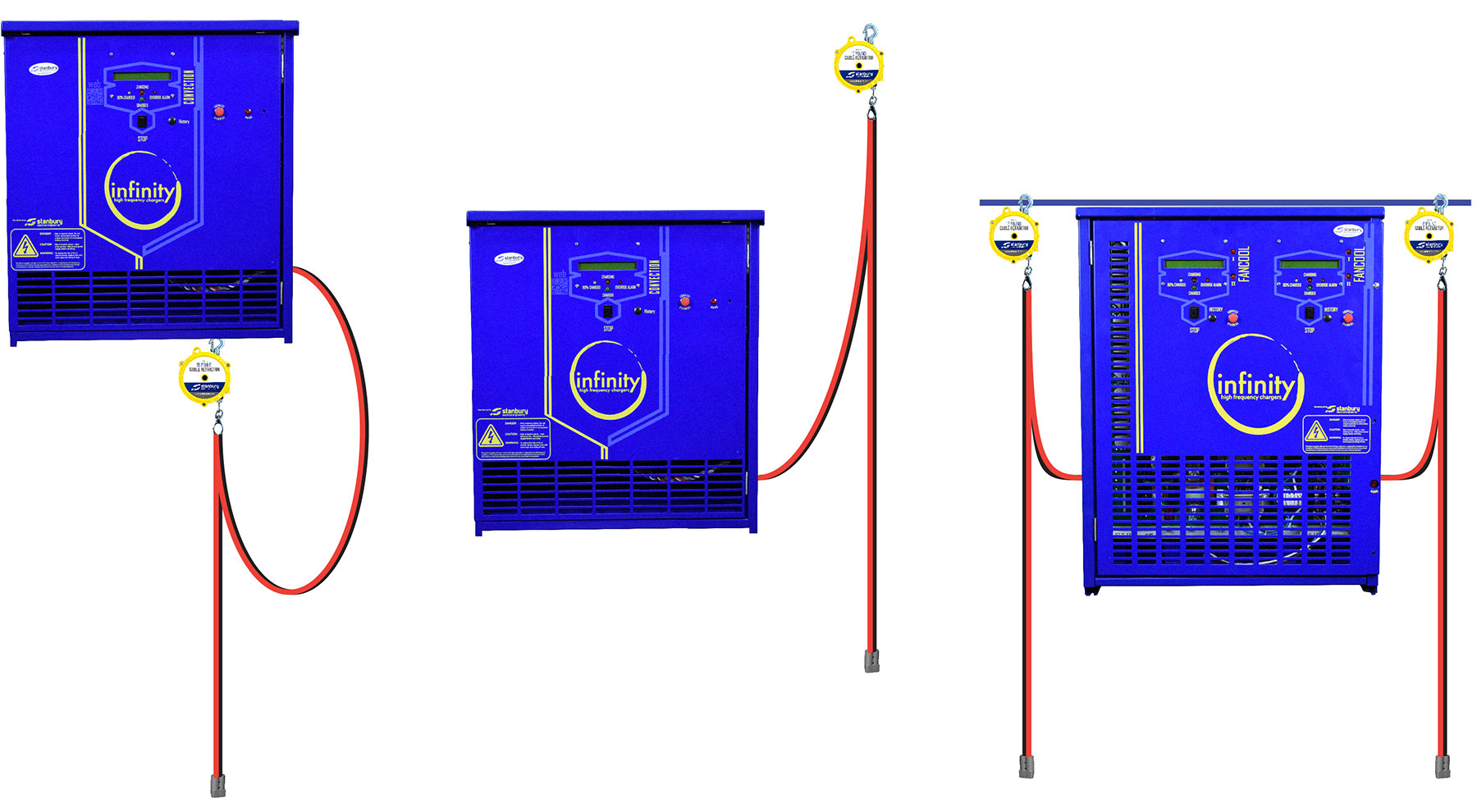
Once the cable retractor is mounted, the cable clamp hanger position needs to be chosen. This is usually between three to five feet from the connector housing, but this will ultimately be determined by maximum potential extension travel, where the cables will sit when retracted, and where the battery is positioned while charging.
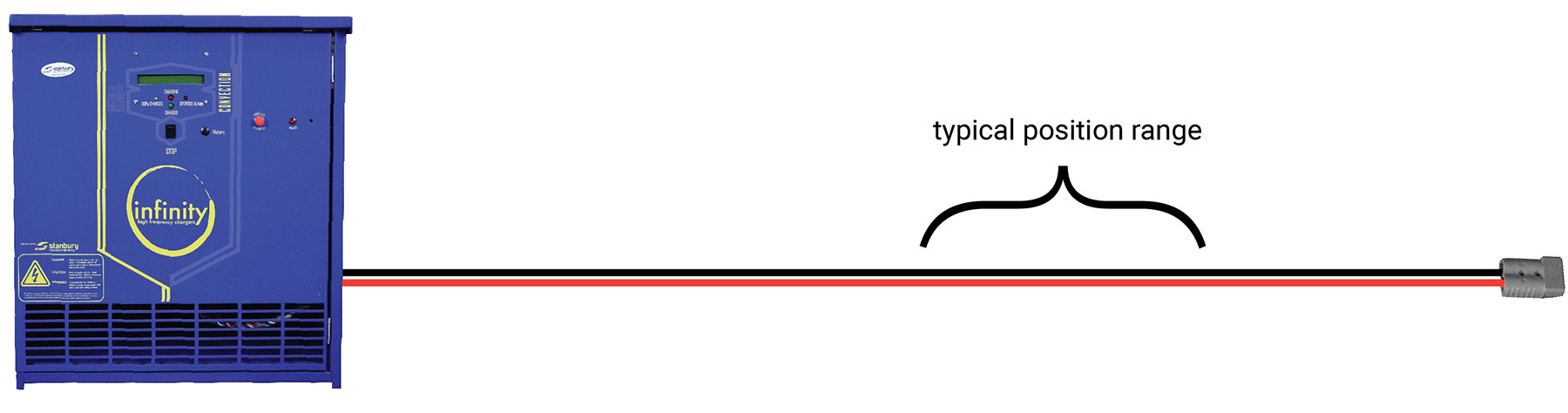
From there the retractor spring tension needs to be adjusted for your specific use case. It should be just enough that the cables are drawn all the way back up, but not so much that it places undue tension on the connector while charging or retracts violently when released.
A successful install will keep your charging cables off the floor, tidy, and out of harm’s way so your operation can enjoy lower maintenance costs associated with battery charging, better operator safety, and a more orderly workplace.
Check out our gallery for TBR-15 cable retractor installation ideas.
Also consider:
- Stanbury Charger Pedestal Stand: safely and securely elevates the charger for charger protection, display visibility, and control access
- Zip Opportunity Charger: the ideal opportunity charging combination for optimizing your fleet’s productivity in busy facilities
- Alkali Lithium Charger: super fast charging for high demand applications
Looking to upgrade?
Contact our friendly experts to see how the TBR-15 Cable Retractor will improve your specific facility’s charging solution.